
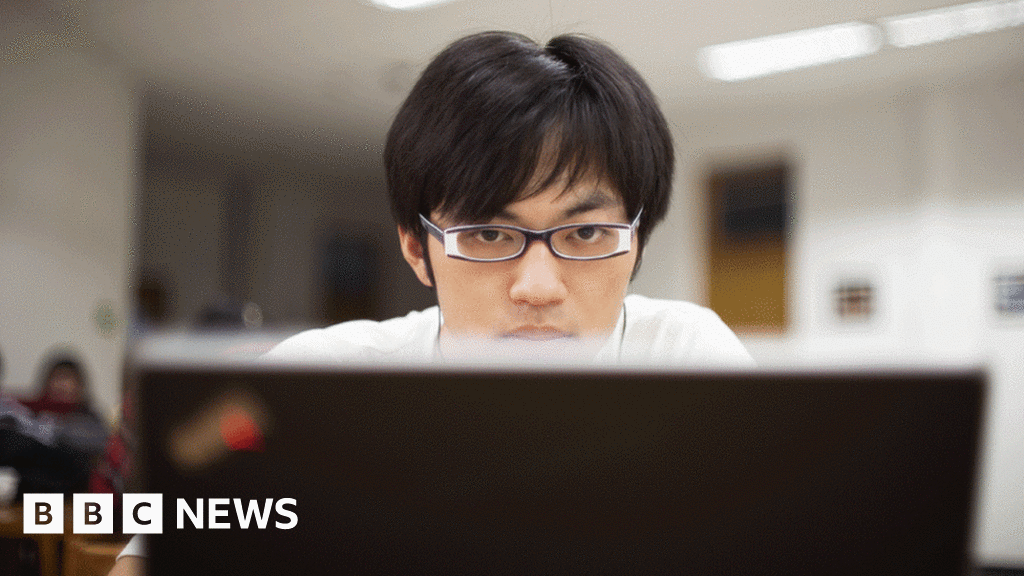
A test on a 100mm thick weld will therefore require a specimen measuring 100mm thick, 200mm wide and 920mm long - an expensive operation, the validity of which can only be determined once the test has been completed. A notch is machined at the centre and then extended by generating a fatigue crack so that the total 'defect' length is half the depth of the test piece- see Fig.1. If the specimen thickness is defined as 'B', the depth (W) will be either B or 2B with a standard length of 4.6W. There are two basic forms - a square or a rectangular cross section specimen. The test piece itself is 'proportional' - the length, depth and thickness of each specimen are inter-related so that, irrespective of material thickness, each specimen has the same proportions. Conventionally three tests are carried out at the relevant temperature to ensure consistency of results.
#Parts and vendors crack full
Unlike the inexpensive 10mm by 10mm square Charpy-V test piece with a blunt machined notch, the CTOD specimen may be the full thickness of the material, will contain a genuine crack and will be loaded at a rate more representative of service conditions. The CTOD test is one such fracture toughness test that is used when some plastic deformation can occur prior to failure - this allows the tip of a crack to stretch and open, hence 'tip opening displacement'.
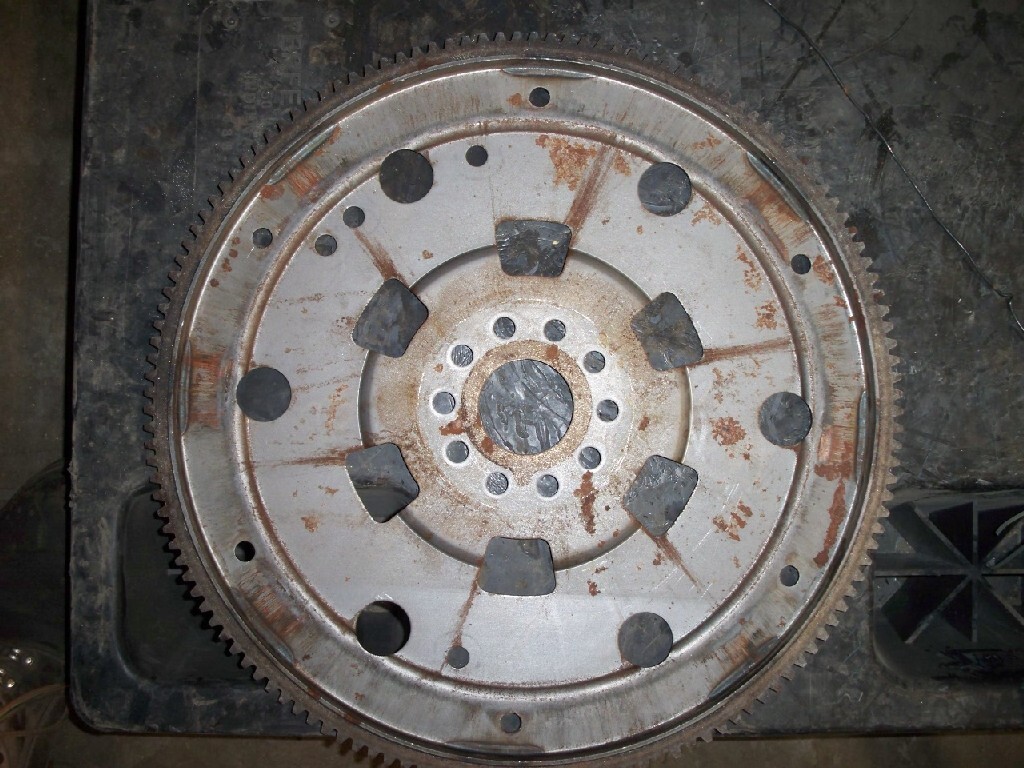
Whilst the Crack Tip Opening Displacement (CTOD) test was developed for the characterisation of metals it has also been used to determine the toughness of non-metallics such as weldable plastics. Such engineering critical assessments can save an operator large amounts of time and money, running into perhaps hundreds of millions of pounds in the case of an oil rig for example.
#Parts and vendors crack cracked
Thus, prior to fabrication, realistic acceptance standards can be set and decisions on appropriate NDE techniques and detection sensitivities can be made.įor equipment already in service, it is possible to justify the continued use of cracked or otherwise flawed components until such time as repair or replacement can be effected.
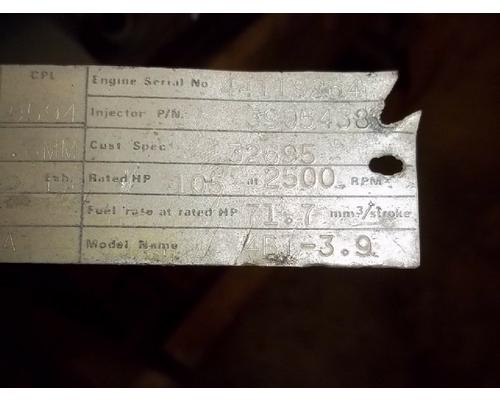
This allows a fitness-for-purpose analysis to be carried out which enables a critical defect size to be calculated.
#Parts and vendors crack full size
The next few articles will look at the tests that enable fracture toughness to be accurately measured in a quantitative manner by using a full size specimen containing a crack with loading that is representative of service conditions. The concept of fracture toughness was introduced in an earlier Connect article, Job knowledge 71, which discussed the Charpy-V test, a simple qualitative test that gives only an indication of the toughness of a metal.
